差分点検をはじめとした設備管理のDXに貢献することへの期待大
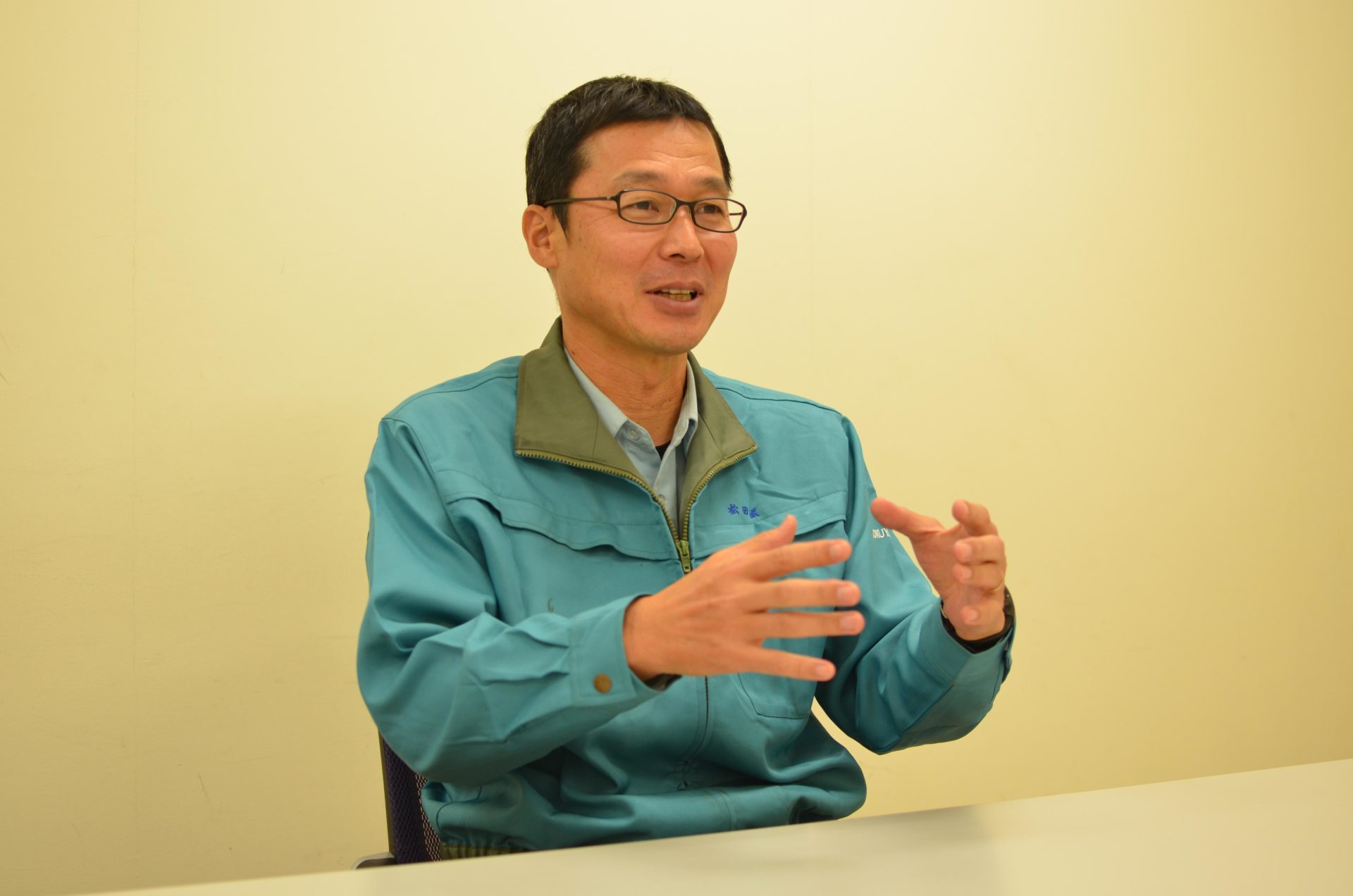
株式会社トクヤマ セメント製造部 設備保全課 松田弦也氏
山口県周南市に製造拠点を置く株式会社トクヤマは、1918年にソーダ灰の国産メーカーとして創業して以来、セメントやさまざまな化学製品を製造している総合化学企業です。セメントを製造している徳山製造所では、セメントの原材料となる石灰石を焼成してクリンカーを作る、ロータリーキルン(回転窯)と呼ばれる装置が3系列あり24時間連続で稼働しています。こうした連続操業型のセメント工場では、このキルン1系列ごとに1年に1回、プラントを停止し、各機器の点検と保守を実施。同社ではこの点検作業にIBISを試験的に採用しており、今回はそんなトクヤマのIBISを使った点検について紹介します。
複数のサイクロンに架設する特殊な足場のコストが課題
セメントは原料となる石灰石を細かく砕いて焼くことで作られます。セメント原料は約1450℃に熱せられた巨大なロータリーキルンの中で焼成されますが、このキルンに投入する前に、あらかじめニューサスペンションプレヒーター(予熱装置)で予熱されます。この装置は複数のサイクロン(固気分離装置)で構成され、キルンで発生した高温のガスにセメント原料を投入することで加熱するというものです。この中ではガスと原料との混ざった気体が分離されガスはさらに上のサイクロンへ、原料はさらに下のサイクロンへ進みながら原料を加熱していきます。
サイクロン内部のガスはセメント原料が混ざった気体のため、その内部にある内筒と呼ばれる鋼製の筒が徐々に摩耗していきます。サイクロン内筒を取り替えてから数年はマンホールから人が覗いて見える範囲で点検し、取替時期の前にサイクロン内部に足場を設置して状態確認、点検をしています。ただし、サイクロンの内部はすり鉢状になっているため、一般的な足場は設置できず、特殊な足場を使用するため、その架設にはとても手間と費用がかかることが課題となっています。
また、ニューサスペンションプレヒーターは複数のサイクロンが縦に積みあがったような形で、その高さは80mにもなります。「点検者が高所で作業することになり、転落などの災害が起こるリスクがある。さらに、サイクロンの内部はとても狭いうえに、セメント原料を扱っているため粉塵環境となり作業の環境としても厳しい」(松田氏)といいます。
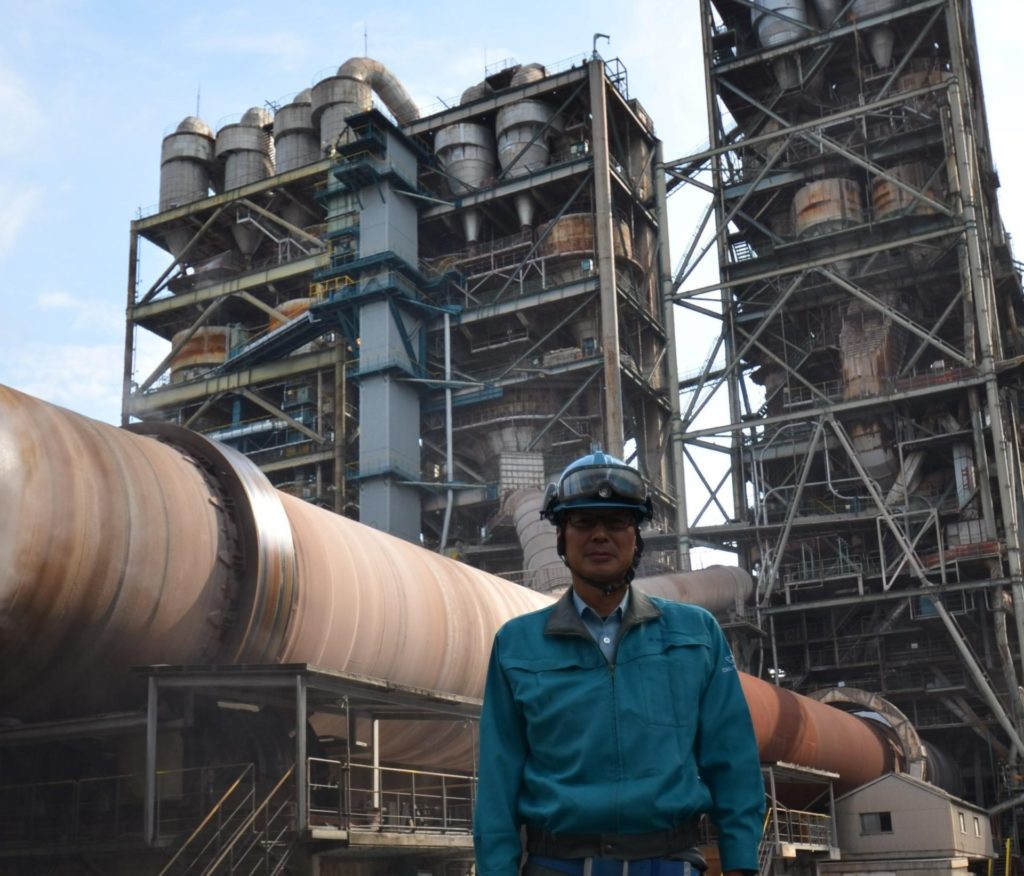
松田氏の奥に立つのが3機のニューサスペンションプレヒーター。逆円錐状のサイクロンが何段にも積み重なっていることがわかる。
現場の状況を可視化して設備の状態を全員で情報共有することができる
トクヤマでは数年前から新しい技術を導入することで安全性と効率性を追究し、労働人口の減少といった環境変化にも対応しながら安定生産を目的とした、設備管理業務のスマート化を進めており、そんな新しい技術のひとつがドローンを活用した設備点検です。屋外にある設備の外面の点検については、設備保全課の課員が自らドローンを操縦して点検を行う試みを行ってきました。しかし、サイクロンの内部といった狭小空間でドローンを飛ばして点検を行うには一般的なドローンでは難易度が高く墜落のリスクも高まります。そこで、狭小空間や粉塵環境といった厳しい環境下でも飛行できるIBISに目を付けたのです。
当初、試験的に二度、実際の現場でIBISを飛行させて、狭小空間、粉塵環境で問題なく飛行できるかを確認し、導入を決定。2022年度からサイクロン内部を中心に、リベラウェアに飛行を依頼する形で、点検を行っています。「リベラウェアのオペレーターはIBISの操縦技術に優れていて、必要な映像を抜けなくきめ細やかに撮影してくれる。また、現場のモニターで確認しながら“ここが見たい”といった我々の要望にも直ちに対応できる。こうした安心感に加えて、最初の相談から作業まで約1か月というスピード感もあり満足している」(松田氏)。
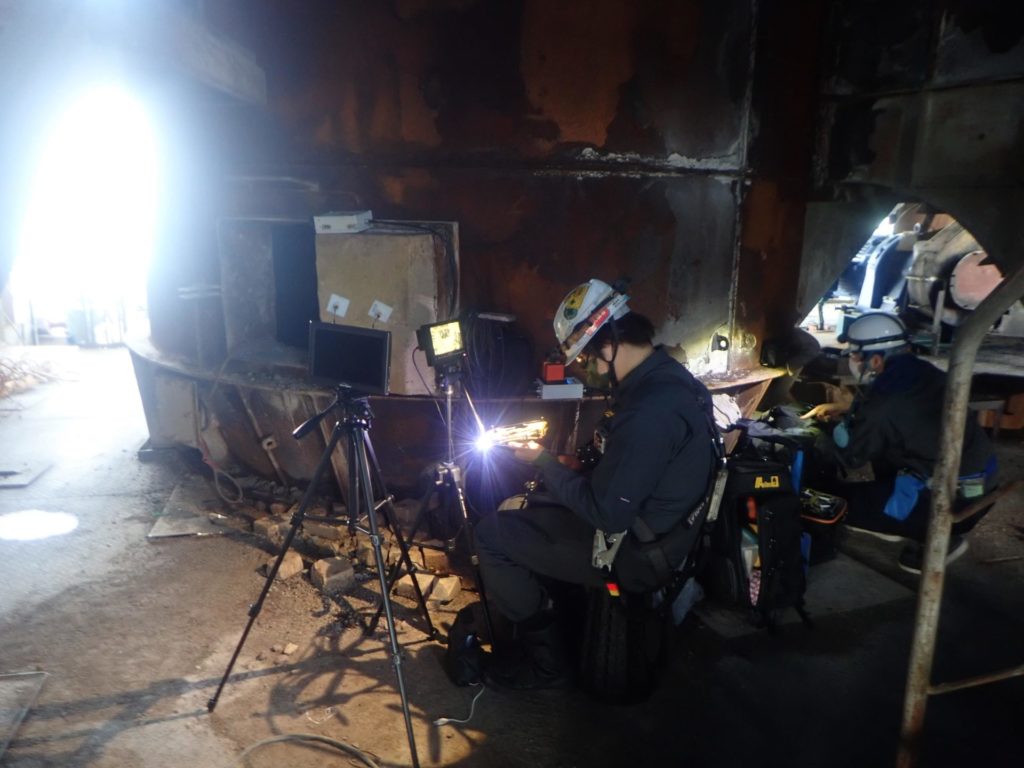
IBISを使ったサイクロン内部の点検の様子。側面のマンホールからIBISを内部に進入させる。
また、点検の工期や費用面でのメリットも実感していると松田氏。「IBISによる点検は全体の作業の中のひとつという位置付けではあるが、ドローンによる工期短縮によって後の工程が前倒しできるなど、トータルで工程の短縮につながる可能性はある。また、費用面ではこれまでサイクロンの内部に設置していた特殊な足場を架設しなくていいというコストメリットは大きい。サイクロンは1基のニューサスペンションプレヒーターに10基近くあり、それがさらに3系列あるため費用はさらに大きなものとなる」(松田氏)からだといいます。
IBISを使って撮影したデータから三次元データを生成し、画像解析をするなど、これまでの目視点検ではできなかった設備の管理ができることも松田氏は評価。「網羅的に撮影した動画から、三次元PDF、オルソ画像を生成してもらっているが、現場の飛行から1ヶ月程度でデータを受け取れるというスピード感にも満足している。また、データを可視化できることで、“今、設備はこんな状況にある”ということを正確に伝え全員で情報共有することができる」(松田氏)のも導入効果の一つとして挙げています。
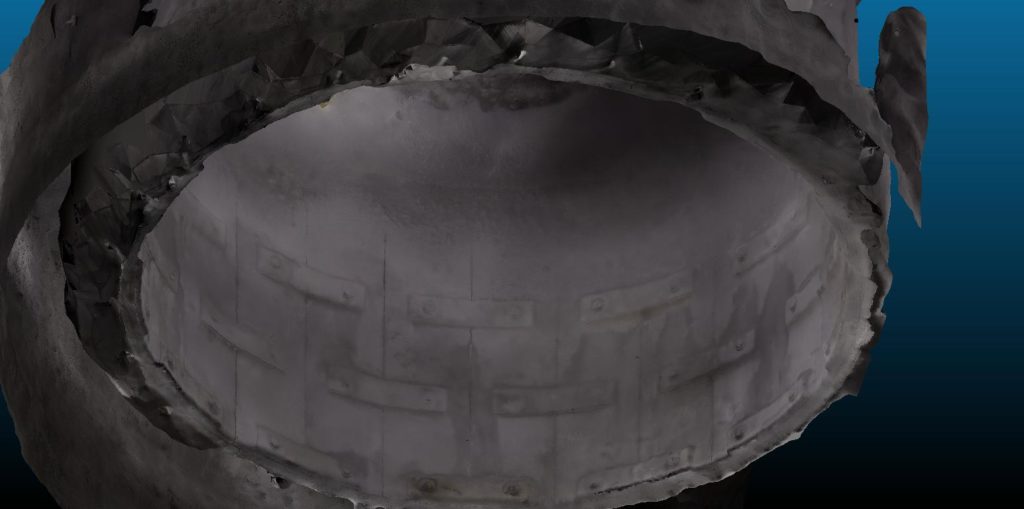
IBISで撮影した映像から生成したサイクロン内部にある内筒の三次元モデル

設備の管理をTBMからCBMに移行することができるドローン点検
さらに、これらのデータは単に現場の状況を1枚の画像として確認できるメリットだけでなく、定期的に点検してこれらの画像を積み重ねていくことで、劣化の進み具合を管理することが可能になります。「半年前の点群データと今回の点群データを重ねることで、サイクロン内部部品がどの程度摩耗しているかをより正確に評価できるようになれば、より確度の高い部品取替時期を導き出すことができる」と松田氏。
トクヤマではこれまで、目視点検の知見、過去の経験値に重きを置いてサイクロンの保全周期を決めるTBM(時間基準保全)で保全を行なっていたといいます。「正確な部品の寿命がわかるようになれば、より計画的な保全の立案が可能となり、設備の管理をTBMからCBM(状態基準保全)に移行することにつながる。より計画的な保全が可能となり、保全コストの低減につなげることができる」(松田氏)としています。
今年度からニューサスペンションプレヒーターのサイクロン内部に対するドローン点検を導入したトクヤマ。「職人が年々減ってきている、未来永劫、設備に足場を架設して点検を行うスタイルを続けるかが課題ではあるが、直ちにそうした点検のすべてがドローンによる作業に置き換わるわけではない。しかしセメント工場内には高所、狭小空間、粉塵環境といった点検作業が困難な場所が多数あり、今後もドローンを使った点検に置き換えていくことに意義がある」と松田氏は締めくくりました。